Here is an example of Rohloff customer service.it is a copy of a post my friend made a few years ago. The problem was nothing to do with the hub but the bike a Surly Troll which did not have the correct axle plate. He now has a Nomad.
Raymond's story
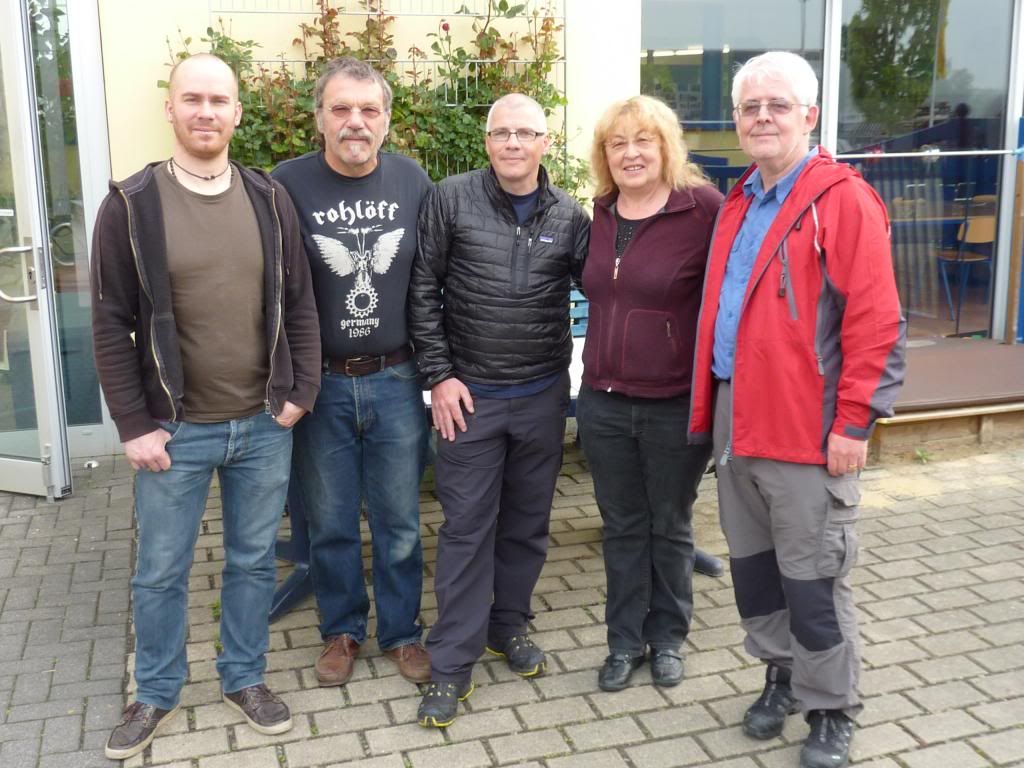
First thing's first, a big thank you to Stuart, who played a blinder and made the visit to the Rohloff factory, a complete pleasure.
Stuart amongst all the other things, deals with the English speaking customers and makes the whole process seamless.
Great to see customer service at the top of the list and not a dying art that you get with other companies.
Also dealing with someone who knows the product inside out, only inspires confidence in the Rohloff brand.
Bob & I, on our annual overseas trip had flown to Basal in Switzerland, 8 days previous, before boarding a train and boat towards Lindau in Germany
We would spend the following days cycling the Bodensee Konigssee Radweg, past some of the best alpine scenery.
Although we had taken camping equipment, we were fortunate, not to have used it.
Instead we stayed in Hostels, Pensions & Gasthaus.
Enroute my Rohloff had developed some slippage when gears 4, 6, 7 &11 were selected and although it did not affect the trip, it was more of an annoyance.
Prior to the trip I had replaced my shifter and converted my Rohloff to an EX box and was unsure if this was the reason.
On completion of the route and with 2 days left before flying out from Munich, we decided to email Rohloff with my concerns and see if they would they have a quick look at my hub, if we just turned up.
I left my phone number and stated that if it was okay could they call me as we would be onboard the train and making the 400 mile journey, from Berchestgaden to Kassel
Sure enough, enroute I received a call from Stuart and was advised to turn up and the mechanics would give it the once over and whilst that was being carried out, Stuart would give us a guided tour around the factory.
As we arrived in Kassel at 1600 hours on the Monday the factory would be closing soon and staff would be heading home.
We headed for the Kassel Youth Hostel, before making the 6km run out to the factory in Fultadal, so we would know the route on Tuesday morning as time was of the essence as we had to make sure we were in Munich Airport for 1900 hours for our flight home.
Tuesday morning we were on the Rohloff door step at 0645, just as the staff were rolling in.
Stuarts expecting you, grab yourself a coffee, he'll be in at 0700.
Needless to say my Rohloff was fixed, some new seals fitted and an oil change done.
Stuart, after explaining his role in the company, took us through the whole Rohloff build procedure, from axle to completed hub.
Having worked in the shop floor at the start of his career with Rohloff, he made short work of the build process.
We can now appreciate, why the Rohloff costs what it does after seeing its inner workings.
All parts made in Germany, with exceptional tolerances at every stage of the build.
An hour and half later and on our departure, the bossman and his wife made an appearance.
We'd like to think, that he heard we were in town, but in reality, we think that he likes to keep a hands on approach to his creations.
Mrs Rohloff gave us some Rohloff stories books.
All in all a great end to a cracking trip.